|
|
|
|
|
|
CHEMICAL INDUSTRIES |
|
|
|
|
|
1. Car Polish |
|
Car polishes mainly serve for cleaning of car paint, to make it shine and to improve its anti-adhesion behaviour. Polishes are partly emulsions and partly suspensions. Their main ingredients are solvents on the basis of mineral oil, water, waxes, tensides as well as finest abrasives like silica or kaolin. The solvents are more and more replaced by aqueous phases. |
|
|
|
Productions in a batch process |
|
|
|
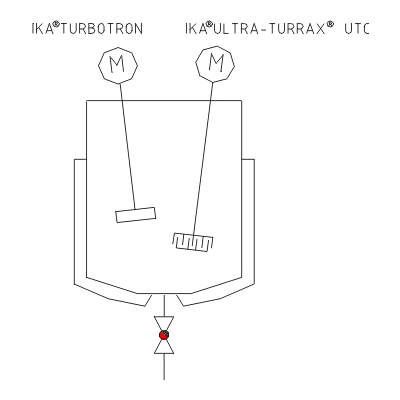 |
|
|
|
Car polishes are mainly produced in batches in following process steps:
- Melting of the wax under slight stirring with an IKA® TURBOTRON®, at a temperature ot approx. 95°C.
- Addition of hot water while strongly emulsifying with an IKA® ULTRA-TURRAX®. Type UTC or UTE.
- Addition of the silicone oil
- Add emulsifier and maybe stabilizer and continue emulsifying intensively with UTC or UTE
- Slowly add abrasives like silica or similar, while stirrer and UTC are still running.
- As soon as homogeneity is reached, the UTC is switched-off and only the stirrer continues running.
- The mixture is cooled down to 30° - 35°C as quickly as possible.
- Car polishes on an aqueous basis (approx. 60% H2O) with a higher silicon content are produced in a similar way. Their emulsification is done with a higher shear rate, thus needing a higher energy input.
|
|
|
|
Productions in a batch process |
|
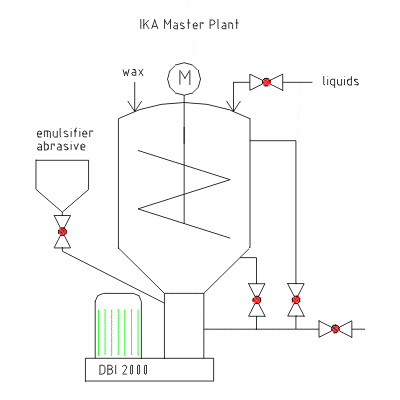 |
|
Production with IKA® Master Plant MP: |
|
- Wax is one of the ingredients of car polish. This wax has either to be melted in a separate melting vessel, or together with the silicon oil, olein, stearic acid and maybe petroleum in the mixing vessel of the IKA® Master Plant MP (temperature approx. 85°C).
- Pre-heated water (approx. 60°C) is mixed into this mixture, resulting in an O/W-emulsion.
- Abrasives, e.g. finest ground kaolin, are added and dispersed. Finally the emulsion/suspension is cooled down to approx. 40°C.
|
|
Back to top |
|
|
|
2. Shoe Polish |
|
Shoe polish is mainly used for two reasons:
|
|
|
|
- To protect the leather against harmful environmental influences
- To give the shoe shine and colour.
|
|
Shoe polish is a typical wax emulsion which is either free of solvents, but may also contain solvents like e.g. solvent naphtha. Major components are different waxes, e.g. paraffin, demineralized water, maybe glycerine, hardeners, colorants and, if necessary, solvent naphtha to influence the drying time and increase the cleaning effect. Solvent free polishes have to be preserved.
|
|
|
|
Productions in batch process |
|
|
|
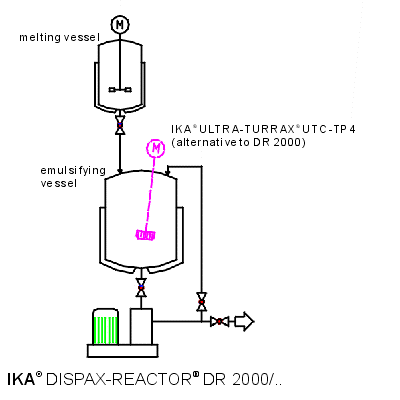 |
|
The production process may look as follows:
- Generation of a wax melt in a melting vessel, maybe also with a certain content of resins like balsamic resin and a non-ionic emulsifier at a temperature of approx. 110°C, under stirring with a disk stirrer at moderate speed.
- This melt is emulsified into potassium hydroxide containing water of approx. 90°C and at the same time cooled down to 60 - 70°C. A hardener may be added. In order to improve the polishing capacities and as a protection against humidity, 5 vol% of the water can be substituted by a silicone emulsion. If necessary, a preservative can be added.
- For stabilizing the emulsion can be cooled down to approx. 50°C, as long as the flow behaviour is not too much impaired.
- As emulsifying machines we recommend IKA® ULTRA-TURRAX® UTC or IKA® DISPAX-REACTOR® DR 2000 for a circulating batch process.
|
|
Back to top |
|
|
|
3. Alumina slurry |
|
Alumina (Al2O3)-slurry mainly consists of water, alumina and the one or other additives. They can be well mixed and dispersed. Due to the very different densities of the main phases there is the danger of sedimentation. Therefore high viscosities are generally adjusted. Moreover strong and turbulent dispersing is necessary. Typical applications for alumina slurry are: diluting agents, catalyst carrier, decolouring agent, polishing agent. |
|
|
|
Productions in a batch process |
|
|
|
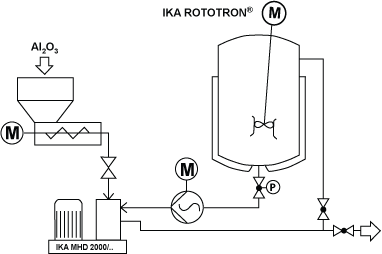 |
|
Production in a batch process with IKA ® Master Plant |
|
- Generally slurries are produced in a batch process.
- It can also be made in a circulating process using an IKA® inline machine of type MHD 2000/.., alternatively in a batch process using an IK® ULTRA-TURRA® UTC. For solids concentrations exceeding 45% the MHD machine is recommended for faster and better wetting of the solids.
|
|
Back to top |
|
|
|
4. Fabric softener |
|
Fabric softener containing cationic tensides, which is added to the last rinsing cycle, will cover the fibre like a film. The tissue will dry faster, and becomes fleecy, soft and smooth. Fabric softeners based on esterquats are more and more used, especially for ecological reasons. Except fragrances these mixtures do not contain anything else but water and electrolytic salts for reduction of the viscosity. For increase and stabilization special, higher-grade esterquat compounds are used. The choice of the production process is also of influence.
The TEA-esterquats belong to the group of cationic fabric softeners. For concentrations up to about 20% lower-grade esterquats are used, which are produced in a batch process. There is an uncontrolled sensitivity for shear rate, which results in a disturbing viscosity increase in the subsequent conveying by pumps.For concentrations exceeding 20% the production in a continuous inline process is recommended, for which higher-grade esterquats are used for higher concentrations. |
|
|
|
Productions in a batch process |
|
|
|
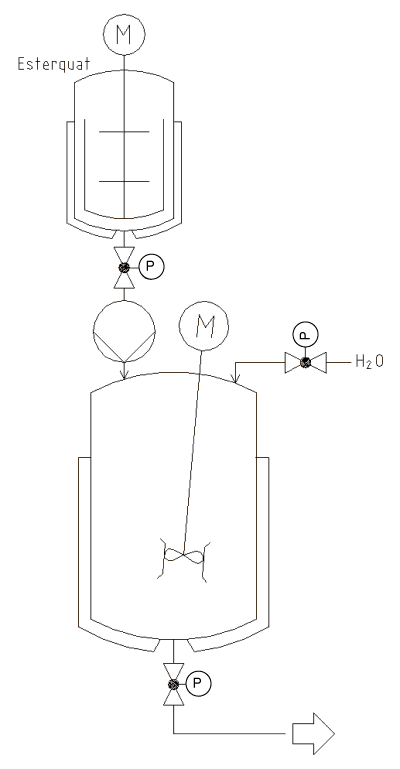 |
|
- The esterquat is heated in a dosing vessel up to 50°C and stirred at the same time by means of an anchor stirrer, in order to improve the heat exchange.
- In the mixing vessel itself water is also heated to 50 - 55°C and convected by means of a jet tube agitator, e.g. type IKA ROTOTRON®, at half speed for better heat distribution. As soon as the set temperatures are reached, the esterquat is added and the speed of the jet tube agitator is increased to the maximum.
- Esterquat and water are mixed until a stable viscosity is achieved. This can be seen from the power consumption.
|
|
Back to top |
|
|
|
5. Furniture polish |
|
Furniture polishes are mainly used for cleaning and polishing of furniture surfaces, but also in order to protect them from environmental influences like humidity. Moreover, they are of course also used to make them more beautiful and to give them shine. Polishes are partly emulsions and partly suspensions. Their main ingredients are solvents on the basis of mineral oil, water, waxes, tensides as well as finest abrasives like silica or kaolin. The solvents are more and more replaced by aqueous phases.sumption. |
|
|
|
Productions in a circulating batch process |
|
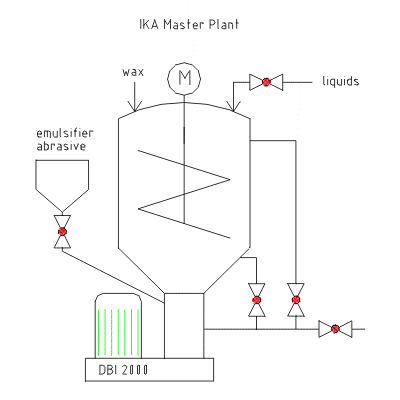 |
|
Production with IKA Master Plant: |
|
- Depending on the type of wood and its surface condition, i.e. treated or untreated, different recipes are used. Hereafter we describe a general recipe and its production procedure.
- Since it is nearly always necessary to heat at the beginning of the process and to cool at its end, the IKA® Master Plant is a very suitable machine and the process can look as follows:
i. approx. 75 parts of a special naphta mixture are heated to 50°C
ii.
approx. 5 parts of polymer SL are solved in this mixture,
iii.
then approx. 4 parts of silicon oil,
iv.
approx. 10 parts of isopropanol,
v.
approx. 5 parts of pine oil and
vi.
approx. 1 part of emulsifier are mixed in.
- Additionally to the vessel the agitator is a also heated for an optimum temperature guiding. The mixing and dispersing machine IKA® DBI 2000 is working at half speed and the temperature is constantly kept at 50°C.
- For recipes containing waxes the process is started with a melting temperature between 70° and 120°C. After all ingredients have been added, the mixture has to be cooled down to approx. 35°C. At this temperature the polish is still flowing, but nevertheless well stabilized.
|
|
Back to top |
|
|
|
6. Silicone Emulsions |
|
Silan- or silicone emulsions are used for multiple purposes. In the cosmetics industry they are used for the production of gels and emulsions. Silicones are synthetic polymer compounds in which silicium atoms are bound in a netted way via oxygen atoms or chains. Remaining valences of the silicium are saturated by residual hydrocarbons. Silicones are something between inorganic and organic compounds, especially between silicates and organic polymers. Silicone emulsions are specially used for creams and sun protection products.
|
|
|
|
Productions in an Inline Process |
|
|
|
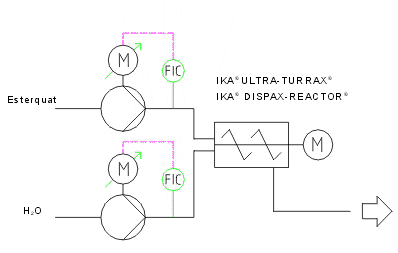 |
|
Production of a silicone / water-emulsion
- It is recommended first to make a preparation with little water (approx. 15%) and to produce a gel-like emulsion. The suitable machine for this purpose is a colloid mill of the type IKA ® MK 2000 with a stronger motor (approx. 30 kW, 1.000 l/h). Moreover it has to be worked with high shear gradient.
- As soon as a homogeneous, transparent and very viscous mixture is reached, any requested viscosity can be adjusted by further mixing in of water and emulsifier.
|
|
Back to top |
|
|
|
7. Talcum suspensions |
|
Talcum is a hydrated magnesium silicate with hydrophobic character and good capacity for absorption of organic substances. It is used in many varieties, from slip additives in technical applications to thickeners or stabilizers in pharmaceutical and cosmetics industry. Especially in paper production talcum is used in coating slips for glossy paper.
|
|
|
|
1. Productions in a Batch Process |
|
|
|
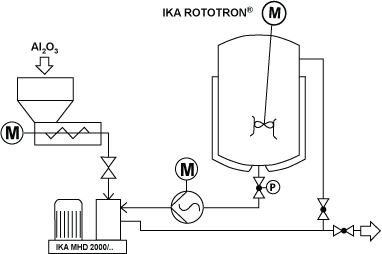
|
|
Talcum has a very low apparent weight, i.e. it tends to swim on the surface of the water and to form lumps. Therefore one should try to incorporate and wet the powder as quickly as possible. The right machine for this purpose is the IKA® mixing and dispersing machine of type MHD 2000/.... In case of very high concentrations an additional wetting aid is used to change the surface tension of one phase. |
|
Back to top |
|
|
|
8. Carbopol dispersions |
|
The Carbopol® polymer can be easily wetted. It is very small-grained and tends to agglomeration when slowly stirred. It is therefore recommendable to add the Carbopol® slowly into the vortex under intensive and turbulent stirring. Isolated small fish eyes are soaking after a certain period of time. For this reason Carbopol®-premixes are often produced separately and in advance in order to enable certain residence times.. |
|
|
|
Processing in a batch Process |
|
|
|
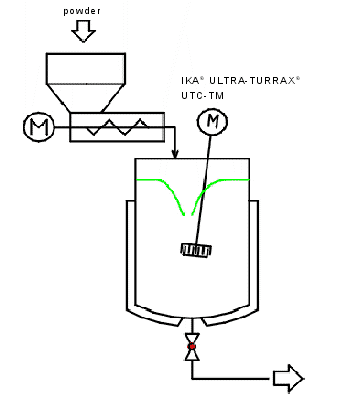 |
|
- Aqueous Carbopol® dispersions are normally produced in a batch process. Their concentrations are between 2% and 5%.
- Carbopol® is a very light powder. It is therefore important to create a good vortex by means of a stirrer, e.g. IKA®-ROTORON®, into which the powder is slowly fed, so that a quick wetting can take place.
- It is recommendable to let the stirrer run slowly for a certain time after feeding of the powder in order to deaerate and neutralise and to soak still existing fish eyes.
- The batch is often left overnight and stirred again shortly before using it.
- Compared to the use of normal stirrers an important time reduction can be reached using an IKA®-ULTRA-TURRAX®.
|
|
Back to top |
|
|
|
9. Bentonite suspensions) |
|
Bentonite is a naturally available aluminium silicate - also called alumina - which is able to absorbe water in a quantity corresponding to many times its own weight. This results in a colloidal suspension, which, depending on the concentration, may become more or less thixotrope. |
|
|
|
Productions in a Continuous Process |
|
|
|
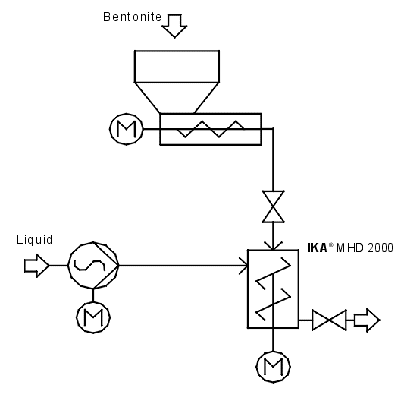 |
|
- For big production quantities it is recommendable to use an inline system, in which the powders are immediately and thoroughly wetted, so that a forming of lumps is avoided from the begining. This aim is perfectly reached with the inline mixing and dispersing machine type IKA® MHD 2000.
- The liquid phase, e.g. water, and the bentonite powder are continuously fed into the machine and the powder is immediately wetted, disagglomerated and dispersed. Concentrations with up to 50% bentonite can be produced.
|
|
|
|
Productions in a Combined Process |
|
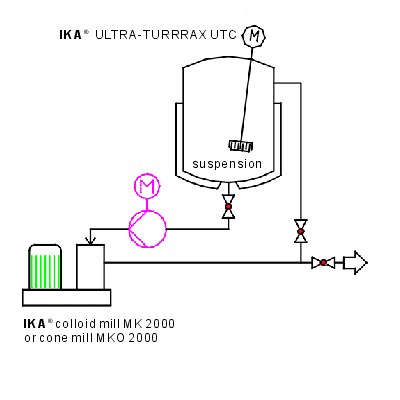 |
|
For the production of very fine bentonite dispersions we recommend to use a combination of IKA® ULTRA:-TURRAX® type UTC and IKA ®. |
|
Back to top |
|
|
|
10. Dilution of WAS (ether sulphate) |
|
Fat containing alcohol-ether sulphates, hereafter called ether sulphates, are the most important tensides for production of cosmetical products like shampoos, shower or bubble bathes and different liquid washing agents. Highly concentrated ether sulphate, e.g. approx. 70%, has a clear gel structure and thus a very high intrinsic viscosity, that may reach some hundreds of mPas. Therefore a high shear rate is necessary to dilute a 70% concentration down to 27% - 28% or even below. Below this concentration a further dilution is very easy. |
|
|
|
Dilution in an Inline Process |
|
|
|
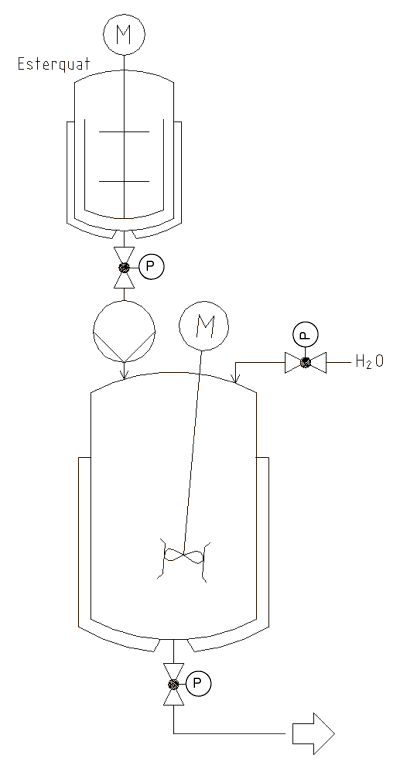 |
|
Production in the IKA ® Master Plant MP |
|
- When water and ether sulphate are brought together, e.g. in a beaker, you will see that gel lumps are formed even under stirring, which are very difficult to be solved again, if ever. It is therefore very important in a dilution process that water and ether sulphate are kept apart as long as possible. i.e. until they directly reach the mixing tool, so that there does not remain any time for gel formation.
- A high shear rate and shear frequency, as e.g. in the IKA ® DISPAX-REACTOR ®; drastically shorten the molecular chain of the ether sulphate. This creates enough surface for the water to settle down, resulting in a dilution of low viscosity.
- The dilution plant type DPv designed by IKA ® is working as an inline system, i.e. that both phases are continuously fed to the DISPAX-REACTOR ® by means of dosing pumps. During only one passage a concentration of approx. 70% is diluted to a clear product free of air bubbles and pinholes with a concentration of approx. 28%.
- This way of production also offers the advantage, that big storage and mixing vessels are no more necessary. Any requested quantity can be diluted within short time and made available for further process steps. On demand a preservative may be added to the water inlet by a dosing pump.
- The electric control can be designed acc. to the customer's requirements. Special attention has to be drawn to the sequence of switching on and off.
- In a clever arrangement the dilution plant can even be used for further mixing, dilution and homogenizing of the final products like e.g. sham-poos and similar.
- The plant is available for capacities up to approx. 30 t/h
|
|
Back to top |
|
|
|
|
|
|
|
|
|
|
|