|
|
|
|
|
|
COSMETIC INDUSTRIES |
|
|
|
|
|
1. Lipstick |
|
Lipsticks are available in most different colours. On the one hand they serve for decoration, but on the other hand they also protect the lips from getting dry. Lipsticks, same as all decorative cosmetics, are only produced in small batches, since colours have often to be changed and due to the short term shelf-life. Castor oil, a major component, has also been used since a very long time for medical treatment. |
|
|
|
Productions in a circulating batch process |
|
|
|
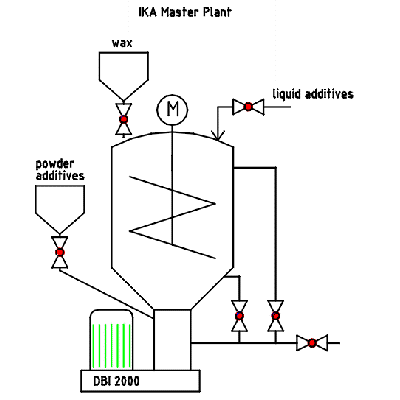 |
|
|
|
The production process for lipsticks may be as follows
- Filling of the double-jacketed mixing and melting vessel with castor oil at room temperature
- Heating is switched-on and heating temperature is limited to 75°C
- Let the stirrer type type IKA ® TURBOTRON ®, which is installed in the mixing vessel, run slowly
- Wax pellets or powder are added via the funnel and melted in the heated castor oil
- Increase the speed of the stirrer
- Pull vacuum and deaerate the melt for about 5 minutes
- Switch-on the IKA ® DISPAX-REACTOR ® DR 2000 or IKA ®-Kolloidmühle MK 2000 and mix the product in a circulation process while controlling the temperature and limiting it to approx. 75°C.
- Add pigments via the funnel, stir for a short time and deaerate again by pulling vacuum.
- Adjust the DISPAX REACTOR ® to full speed and circulate for approx. 10 minutes.
- Add the remaining additives like acetates and glycols while deaerating again and again.
|
|
|
|
When using the DISPAX-REACTOR ® or maybe the colloid mill MK a rather big amount of heat is introduced. Therefore care has to be taken for suitable cooling capacity. It might also be recommendable to install a pump in front of the dispersing machine in order to shorten the residence time. The drive power of the dispersing machines has to be doubled. |
|
Back to top |
|
|
|
2. Shampoos |
|
Shampoos are specially used for hair care. The care effective components are mainly surface active components for cleaning, maybe also for degreasing. The basic materials are demineralized water and lauryl sulphate compounds. The most frequently used additives are substances for conditioning and colouring, scents and shine giving substances, but also preservatives and substances with anti-microbic effect. Most shampoos are adjusted to a pH-value of about 5,5. |
|
|
|
Productions in a circulating batch process |
|
|
|
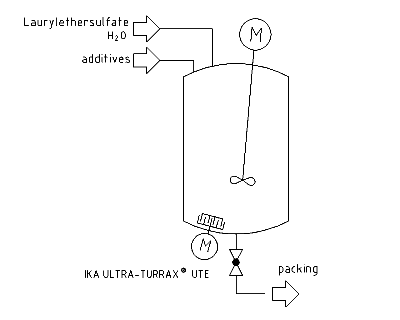 |
|
|
|
- Diluted lauryl ether sulphate and water are given into a vessel and emulsified by moderate stirring.
- Step by step the other components are added. In case of wax like materials the vessel is heated. Depending on recipe and requested homogeneity a rotor/stator machine like IKA ®-ULTRA-TURRAX ® UTE is incorporated in the bottom of the vessel additionally to the normal stirrer. In most cases this rotor/stator machine is working at reduced speed.
|
|
Back to top |
|
|
|
3. Deodorants |
|
Deodorants are substances that shall avoid, cover or remove odours. They are available in different forms: as liquid, roll-on or deodorant spray, as a solid gel in form of a deodorant stick, but also as deodorant cream. |
|
|
|
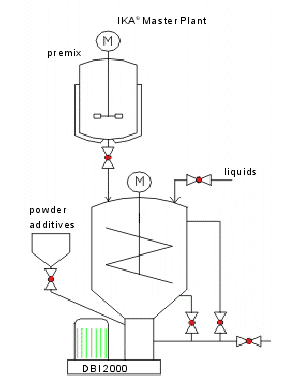 |
|
|
|
Production in a batch process with IKA ® Master Plant |
|
- The continuous phase (alcohols, propylene glycol, glycerine or silicone oil) is prepared in the mixing vessel of the IKA ® Master Plant MP, while the spiral agitator and the dispersing machine of type DBI 2000 are running slowly, and heated up to approx. 50°.
- In a separate vessel the disperse phase is premixed with an IKA ® ULTRA-TURRAX ® and heated. The disperse phase may e.g. consist of cetyl alcohol or hexadecanol compounds (flakes or powders) and maybe thickeners, gelling agents, bentonite as well as water or oil.
- The speed of the dispersing machine DBI 2000 is then increased to normal speed and the premix (disperse phase) is step by step fed into the main mixing vessel. After some time additional active substances, odorous substances (fragrances) and maybe colorants and gelling agents (polymer) are added. During that process the temperature has to be surveyed.
|
|
Back to top |
|
|
|
4. Shaving Products |
|
Shaving products are available as soap, cream or foam. Basically they are produced by saponification of plant or animal fat resp. oil using caustic potash solution and subsequent emulsification with water and different additives. Lanolin or monostearin are added as slip additive and keratin serves for softening of the hair. |
|
|
|
Productions in a circulating batch process |
|
|
|
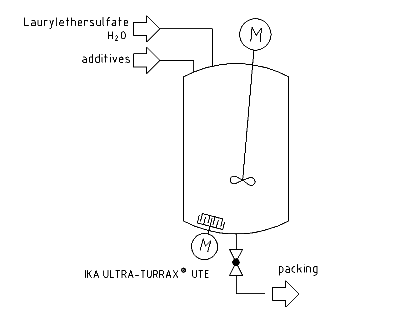 |
|
|
|
Production with IKA ® Master Plant MP |
|
The IKA ® Master plant is very well suited for the production of shaving cream.
The used recipes differ of course from manufacturer to manufacturer, but the production process usually looks like follows: Rapid process time. The intense shear exerted by an IKA® rotor stator mixer ensures that any agglomerates that may form are rapidly broken down, exposing the full surface are of the powder to the liquid. Thus, operators may add powders faster and hydration occurs more rapidly.
- Melting and mixing of the fatty phase in the mixing vessel of the MP at a temperature of approx. 90°C and running spiral agitator.
- In a separate vessel the lye (soda lye or caustic potash solution), water and glycerine are mixed and heated to a temperature of approx. 75° - 80°C.
- This mixture is given into the vessel and emulsified with the fatty phase in circulating operation and at the same time deaerated.
- The remaining stearic acid is added via the funnel as quickly as possible, and the whole mixture is further dispersed under vacuum.
- The remaining additives like fragrances, lactic acid, etc. are also added via the funnel and further homogenized under vacuum.
- The mixture has to be quickly cooled down to 30° - 35°C, while only the stirrer is running. The heatable spiral of the MP-agitator is effectively supporting the cooling procedure
|
|
Back to top |
|
|
|
5. Sun Protection Gel |
|
Gels are similar to the group of colloids. They are shape-retaining, easily deformable, disperse systems of at least two components. They mostly consist of a solid, colloidally split substance (e.g. gelatine, silicic acid or polysaccharides) and water as dispersing agent. Sun protection gels do not only protect the skin against intensive radiation, but also against extreme dehydration. There are recipes using the interior of the leaves of the aloe vera plant, which exists already in form of a gel. |
|
|
|
Productions in a batch process |
|
|
|
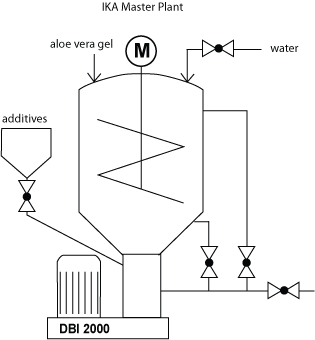 |
|
|
|
A sun protection gel with aloe vera can be produced acc. t the follow-ing procedure:
- Demineralized water and aloe vera gel in relation 1 : 1 are mixed in a vessel; total approx. 75% vol. in the mixing vessel.
- A thickener, e.g. Carbopol, is added
- Propylene glycol and further additives in small quantities are added
- Triethanolamine is added
- Colorants are added
|
|
Back to top |
|
|
|
6. Silicone Emulsions |
|
Silan- or silicone emulsions are used for multiple purposes. In the cosmetics industry they are used for the production of gels and emulsions. Silicones are synthetic polymer compounds in which silicium atoms are bound in a netted way via oxygen atoms or chains. Remaining valences of the silicium are saturated by residual hydrocarbons. Silicones are something between inorganic and organic compounds, especially between silicates and organic polymers. Silicone emulsions are specially used for creams and sun protection products.
|
|
|
|
Productions in an Inline Process |
|
|
|
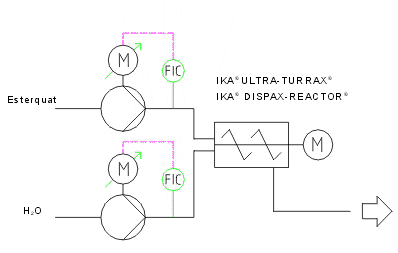 |
|
|
|
Production of a silicone/water-emulsion
- It is recommended first to make a preparation with little water (approx. 15%) and to produce a gel-like emulsion. The suitable machine for this purpose is a colloid mill of the type IKA ® MK 2000 with a stronger motor (approx. 30 kW, 1.000 l/h). Moreover it has to be worked with high shear gradient.
- As soon as a homogeneous, transparent and very viscous mixture is reached, any requested viscosity can be adjusted by further mixing in of water and emulsifier.
|
|
Back to top |
|
|
|
7. Carbopol Emulsionssted by further mixing in of water and emulsifier. |
|
When producing emulsions in the cosmetic industry, e.g. creams and lotions, Carbopol is often used as thickener or gelling agent. Carbopol is carboxyvinylpolymer, i.e. a resin. It is a white powder with hygroscopic characteristics and physiologically harmless. Due to its strong attitude to form lumps, great care has to be taken for its processing.
|
|
|
|
1. Productions in a Batch Process |
|
|
|
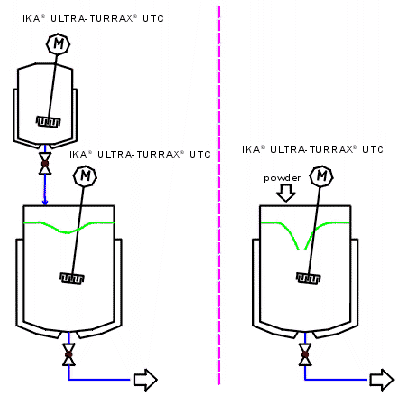 |
|
|
|
- There are two methods of producing Carbopol® emulsions in a batch process: the "direct" and the "indirect" method.
- Working with the "indirect method" means producing a premix with the oily phase (non-solvent). With this method concentrations of up to 30% can be achieved, nevertheless maintaining a good flowability. When this premix is fed into an aqueous phase (with a neutralizing agent) and moderately stirred or dispersed, a smooth emulsion is forming after approx. 20 minutes.
- A suitable dispersing machine is e.g. an IKA® ULTRA-TURRAX® type UTC with variable speed.
- Working with the "direct method" means that the Carbopol® is directly fed into the stirring vortex of the water. Care has to be taken that there are no lumps in the Carbopol® itself. The oily phase is then added under continuous stirring. Thus a shining mixture is produced which has subsequently to be neutralized by means of a suitable lye.
|
|
|
|
2. Productions in a Batch Enrichment Process |
|
|
|
 |
|
|
|
- Carbopol® emulsions can also be produced in a batch enrichment process using the powder incorporation and dispersing machine IKA®-CMS 2000/... The powder is sucked-in via the funnel that is connected to the aspiration socket of the machine, and directly dispersed into the circulating flow of liquid. Thus agglomerations are avoided from the beginning and homogeneous emulsions can be produced in a very short time.
- Special funnel geometries help avoiding a "chimney effect" in the funnel. The incorporation of air is thus restricted to the quantity included in the powder. After incorporation of the solids, the final product can be circulated with the IKA®-CMS 2000/.. for further homogenization.
|
|
Back to top |
|
|
|
8. Processing of Vegetable Oil |
|
Vegetable oils are an important ingredient in many cosmetic products.. Nevertheless, before they can be used, they have to be "degummed".For this purpose proteins, carbides and phosphatides, that cloud the oil and are responsible for conglutination effects, have to be removed. Afterwards free fatty acids, that accelerate the spoiling of the and also influence the taste, are removed by neutralization. The subsequent bleaching not only removes colours but also metals, traces of phosphatides, soaps and oxidation products. |
|
|
|
Processing in an Inline Process |
|
|
|
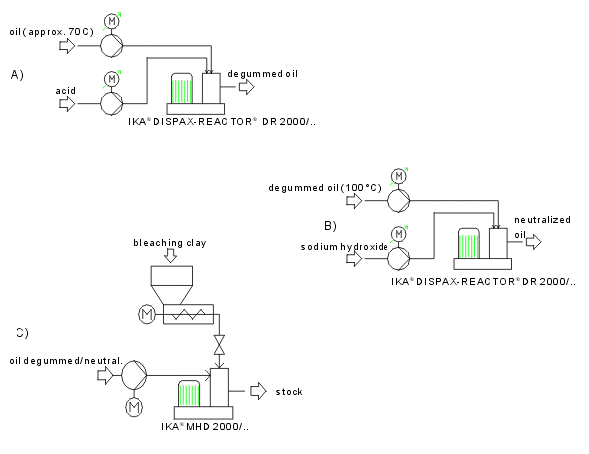 |
|
|
|
Vegetable oils are processed in following steps: |
|
|
|
a). Degumming |
|
Part of the phosphatides in the raw oil are hydrogenizable with water and can thus easily be separated. The remaining non-hydrogenizable phosphatides can be separated by adding acid.
The untreated oil is heated up to 60°C - 70°C and thoroughly mixed with up to 1% of phosphoric acid. The acid is reacting with the phosphatides, thus enabling a settlement of the water. The phosphatides can then be separated by filtration or centrifuging. This results in a "degummed" oil and gum resin, from which, under certain conditions, lecithin can be produced. For a thorough mixing of acid and oil the IKA ®-dispersing machine type DISPAX-REACTOR ® DR 2000 proved to be very suitable. |
|
|
|
b). Neutralization |
|
Free fatty acids (FFA) are influencing the taste of the oil and accelerate its spoiling. For neutralization of the FFA the oil is intensively mixed with sodium hydroxide at a temperature of approx. 90° to 100°C. The FFA are settling as soaps and can be sperated by centrifuging. The DISPAX-REACTOR ® DR 2000 as well as the single stage dispersing machine of type ULTRA-TURRAX ® UTL 2000 proved to be the right machines for neutralization of the FFA. |
|
|
|
c). Bleaching |
|
In order to remove remaining impurities like colour and oxidation products the oil can finally be bleached. For this purpose it is intensively mixed with bleaching clay. For this process we recommend the IKA ® inline mixing and dispersing machine type MHD 2000. |
|
Back to top |
|
|
|
|
|
9. Dilution of WAS (ether sulphate) |
|
Fat containing alcohol-ether sulphates, hereafter called ether sulphates, are the most important tensides for production of cosmetical products like shampoos, shower or bubble bathes and different liquid washing agents. Highly concentrated ether sulphate, e.g. approx. 70%, has a clear gel structure and thus a very high intrinsic viscosity, that may reach some hundreds of mPas. Therefore a high shear rate is necessary to dilute a 70% concentration down to 27% - 28% or even below. Below this concentration a further dilution is very easy. |
|
|
|
Dilutions in an Inline Process |
|
|
|
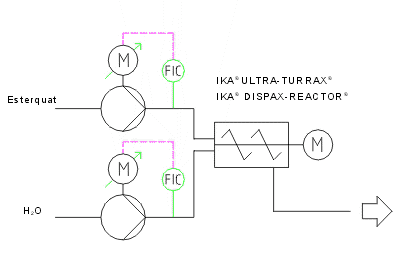 |
|
|
|
- iWhen water and ether sulphate are brought together, e.g. in a beaker, you will see that gel lumps are formed even under stirring, which are very difficult to be solved again, if ever. It is therefore very important in a dilution process that water and ether sulphate are kept apart as long as possible. i.e. until they directly reach the mixing tool, so that there does not remain any time for gel formation.
- A high shear rate and shear frequency, as e.g. in the IKA ® DISPAX-REACTOR ®; drastically shorten the molecular chain of the ether sulphate. This creates enough surface for the water to settle down, resulting in a dilution of low viscosity.
- The dilution plant type DPv designed by IKA ® is working as an inline system, i.e. that both phases are continuously fed to the DISPAX-REACTOR ® by means of dosing pumps. During only one passage a concentration of approx. 70% is diluted to a clear product free of air bubbles and pinholes with a concentration of approx. 28%.
- This way of production also offers the advantage, that big storage and mixing vessels are no more necessary. Any requested quantity can be diluted within short time and made available for further process steps. On demand a preservative may be added to the water inlet by a dosing pump.
- The electric control can be designed acc. to the customer's requirements. Special attention has to be drawn to the sequence of switching on and off.
- In a clever arrangement the dilution plant can even be used for further mixing, dilution and homogenizing of the final products like e.g. sham-poos and similar.
- The plant is available for capacities up to approx. 30 t/h
|
|
Back to top |
|
|
|
10. Emulsions for sun protection spray |
|
Sprayable sun protection emulsions are O/W-emulsions. They are characterised by a special homogeneity and a low viscosity, but nevertheless a good adherence. Contrary to the use of lotions the skin surface is not so much pasted up. |
|
|
|
Production in a batch Process |
|
|
|
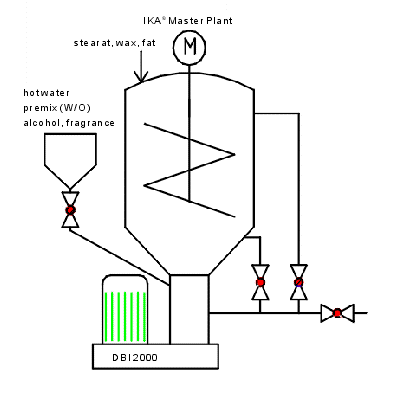 |
|
Production in the IKA ® Master Plant MP |
|
The spray is produced in following steps:
- The mixing vessel is pre-heated to approx. 80°C.
- Stearates, fats and waxes are fed from upside and melted (approx. 27% of the formulation). During that process the spiral agitator is slowly running. The DBI 2000 is also running slowly, in order to keep the material in the lower part of the vessel in movement.
- The polymer is added to the melt.
- Hot water of approx. 80°C (approx. 40% of the formulation) is added via the lateral funnel, while the homogenizing machine DBI 2000 is running with a tip speed of 23 m/s. This quickly creates a W/O-emulsion. After adding the water the material is several times circulated.
- A premix of cold water (approx. 25°C) and the oily phase (approx. 35% of the formulation) is prepared and added very slowly via the lateral funnel, so that the emulsion is converted into an O/W-emulsion.
- The emulsion is then stirred to become cold - approx. 25°C - and alcohols and odorous substances are added via the funnel.
- Finally the emulsion is carefully homogenized and maybe also cooled, so that a temperature of approx. 25°C is not exceeded. IKA ® Master Plant MP
|
|
Back to top |
|
|
|
|
|
|
|
|
|
|
|
|
|
|
|